Esta postagem faria parte do meu novo livro, Tim Cook: o gênio que levou a Apple ao próximo nível, mas foi cortado no comprimento. Ao longo da próxima semana ou assim, iremos publicar várias outras seções que foram cortadas, focando principalmente nas operações de manufatura da Apple.
Steve Jobs sempre teve um grande fascínio por fábricas automatizadas. Ele foi exposto a eles pela primeira vez durante uma viagem ao Japão em 1983. Na época, a Apple tinha acabado de criar uma nova unidade de disquete chamada Twiggy. Durante uma visita à fábrica da Apple em San Jose, no entanto, Jobs ficou irado quando descobriu a alta taxa de falhas dos drives Twiggy que a Apple estava produzindo. Mais da metade deles foram rejeitados. Jobs ameaçou demitir todos que trabalhavam na fábrica
Esta postagem contém links de afiliados. Culto de Mac pode ganhar uma comissão quando você usa nossos links para comprar itens.
Inspirado por Alpes e Ford
Uma alternativa era usar um novo drive de 3,5 polegadas desenvolvido pela Sony e fabricado por um pequeno fornecedor japonês chamado
Alps Electronics. Quarenta anos depois, o Alps continua fazendo parte da cadeia de suprimentos da Apple. Jobs conhecia Yasuyuki Hirose, um engenheiro da Alps que conhecera no West Coast Computer Faire, a primeira exposição de computadores pessoais do Vale do Silício, onde a Apple estreou o Apple II.Em 1983, Jobs visitou a fábrica da Alps no Japão. Na época, o Japão estava experimentando um crescimento econômico surpreendente, em parte como resultado de suas fábricas, que produziam carros, microchips e Walkmans a uma velocidade surpreendente.
De acordo com Yasuyuki Hirose, um engenheiro de unidade de disquete da Alps, “Steve estava particularmente interessado em processos de manufatura. Em 1983, ele fez um tour pela fábrica automatizada em Furukawa e fez muitas perguntas. ” (Alguns anos depois, quando Jobs abriu sua própria fábrica automatizada, ele convidou Hirose para fazer uma visita. “Foi então que percebi o que Steve sempre quis fazer”, disse Hirose.)
Jobs ficou impressionado com o Japão, um país pelo qual sempre teve um caso de amor. No entanto, seu impulso para construir fábricas automatizadas também pode ter sido parcialmente inspirado por um dos heróis americanos de Jobs: o pioneiro do carro Henry Ford.
Os carros da Ford mudaram o mundo não apenas por meio da tecnologia que introduziram, mas também porque eram baratos o suficiente para serem comprados pelas massas. Em sua busca pela manufatura em massa, os carros da Ford foram montados em grandes fábricas, onde as linhas de montagem dividiam o processo de manufatura em etapas repetíveis. Como resultado de suas inovações, um dos carros de Henry Ford pôde ser montado em menos de uma hora.
Fábrica automatizada de Mac
Demorou apenas 26 minutos para construir um Macintosh inteiro na fábrica altamente automatizada que a Apple abriu em Fremont, Califórnia, em janeiro de 1984 - menos de um ano após a viagem de Jobs ao Japão.
Construída em mais de 120.000 pés quadrados, a fábrica em 48233 Warm Springs Blvd custou US $ 20 milhões e foi uma mostra de produção automatizada, projetada com o objetivo de produzir até um milhão de unidades do Macintosh de $ 2.495 cada único mês.
“Temos grande respeito pela manufatura japonesa”, disse o então presidente da Apple, John Sculley. “Decidimos ser um jogador importante em tecnologia de manufatura. Em três anos, queremos ser tão bons quanto os japoneses. ”
Quando a Apple tinha componentes suficientes em seu estoque e a fabricação estava em pleno andamento, uma nova máquina saía da linha de montagem a cada 27 segundos.
George Irwin, um engenheiro que ajudou a planejar a instalação, que foi comparada a uma gigante fábrica de blocos de Lego devido a ter tantas máquinas, cada uma realizando uma tarefa diferente, tinha o objetivo de reduzir isso para apenas treze segundos.
Nenhum outro fabricante de computador conseguiu igualar esse tipo de saída na época. Na fábrica da Apple em Dallas, um Apple IIe era produzido a cada seis minutos e demorava muito mais para ser montado.
“Antes que o Japão ganhe velocidade com os computadores, queremos estar à frente no jogo”, disse Irwin à revista InfoWorld em março de 1984.

Foto: Terrence McCarthy, usada com permissão.
Como a automação funcionava
Cada Macintosh foi montado a partir de oito componentes principais que podiam ser montados de forma rápida e simples. As máquinas viajariam pela fábrica suspensas no teto nas ricas trilhas vermelhas de um transportadora aérea, e os trabalhadores tinham vinte e dois segundos ou menos para concluir sua função antes de passar para nas próximas.
A Apple certificou-se de que nenhum trabalhador tivesse que alcançar mais de trinta centímetros para obter as peças de que precisavam, que eram entregues em cada estação em um veículo de orientação automatizado de um metro de altura.
Cinco dessas máquinas, cada uma custando US $ 30.000, percorriam o chão de fábrica. Suas tarefas eram atribuídas por um olho polaróide que examinava o depósito e emitia um comando ao identificar uma bandeja de componentes que precisava ser transferida.
As próprias bandejas eram enchidas com caixas de cinquenta libras, pelo menos quatro mil das quais estavam empilhadas com dezoito níveis de altura a qualquer momento.
O empilhador de contenedores, outro serviço de entrega automatizado, percorreu a fábrica em uma trilha, colocando os contenedores na posição correta.
Máquinas de inserção automática foram usadas para montar circuitos e módulos nas placas lógicas, enquanto cerca de cento e vinte Computadores Apple, principalmente o Apple II e Apple III, foram empregados como terminais para o processamento de contabilidade e estoque dados.
Pedidos incomuns de Jobs
Jobs pediu que as máquinas fossem pintadas em tons brilhantes e coloridos, combinando com o logotipo listrado da Apple usado na época. Mas depois de passar tanto tempo examinando lascas de tinta, o então diretor de manufatura da Apple, Matt Carter, finalmente as instalou no bege usual.
Jobs percebeu isso durante uma visita à fábrica, escreveu a seu biógrafo, Walter Isaacson, e exigiu que fossem repintados com as cores que ele solicitou. Carter objetou e explicou que a tinta poderia causar problemas para máquinas de precisão, e isso se provou correto quando uma das máquinas mais caras da Apple, pintada de azul brilhante e mais tarde apelidada de "loucura de Steve", parou de funcionar devidamente.
Carter desistiu como resultado do desacordo; “Foi preciso muita energia para lutar contra ele, e geralmente era por causa de algo tão inútil que eu finalmente tive o suficiente”, disse ele a Isaacson.
Carter foi substituído por Debi Coleman, a diretora financeira do Macintosh que já havia ganhado o prêmio anual da equipe por a pessoa que melhor enfrentou Jobs, e logo ela também se viu envolvida em um desentendimento sobre a fábrica pintar.
Jobs pediu ao diretor de arte da Apple, Clement Mok, que transmitisse seu desejo de que as paredes da fábrica fossem pintadas de branco.
“Não se pode pintar uma fábrica de branco puro”, argumentou Coleman, “vai haver poeira e outras coisas por toda parte”.
“Não há branco que seja branco demais para Steve”, respondeu Mok.
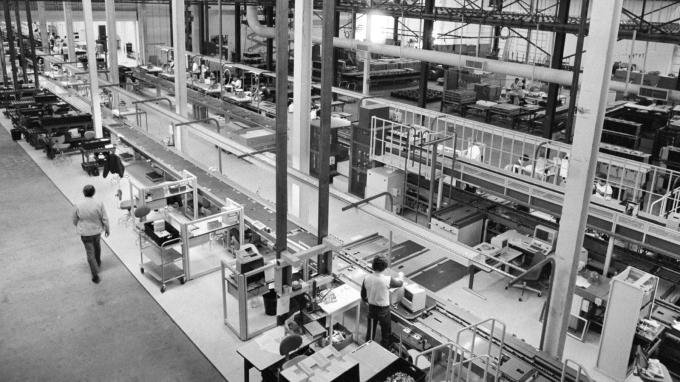
Foto: Terrence McCarthy, com permissão.
A limpeza está ao lado de Jobsiness
Poucos presidentes de empresas ficariam obcecados com a cor de uma fábrica e suas máquinas como Jobs fazia com a instalação do Macintosh.
Ele também queria que fosse limpo e insistia que essa era uma forma de garantir “uma paixão pela perfeição”, escreve Isaacson. “Eu ia para a fábrica e colocava uma luva branca para verificar se havia poeira”, lembrou Jobs. “Eu o encontraria em todos os lugares - nas máquinas, no topo dos racks, no chão.”
Jobs pediu a Coleman que limpasse a fábrica. “Eu disse a ela que achava que devíamos comer do chão da fábrica”, continuou Jobs. "Ela não entendia por quê."
Automação no sentido mais puro
Muito poucas das tarefas exigiam mãos humanas. As máquinas realizaram mais de 90 por cento do processo de montagem, com os trabalhadores intervindo para consertar quaisquer defeitos, como substituir componentes defeituosos ou realizar tarefas que exigiam um toque humano, como polir os logotipos da Apple afixados em cada invólucro.
Um processo de teste rigoroso conhecido como "ciclo de queima", que consistia em ligar cada máquina e desligado a cada hora ao longo de vinte e quatro horas, foi realizado para garantir que cada chip estava funcionando corretamente.
“Outras empresas ligam o computador e simplesmente o deixam parado”, explicou Sam Khoo, gerente de produção da fábrica da Apple à InfoWorld. “Causamos mais estresse aos componentes ao desligá-lo e ligá-lo. Desta forma, os componentes defeituosos aparecerão imediatamente. ”
A instalação de Fremont era “automação no sentido mais puro”, disse Irwin. Menos de noventa trabalhadores eram necessários para cada turno, e eles eram separados por máquinas gigantescas e vastos abismos de espaço, o que significava que havia muito pouco trabalho de equipe.
Em um esforço para evitar que seus empregos se tornassem mundanos e insuportáveis, o que, sem dúvida, levaria à alta rotatividade do pessoal de outras fábricas sofrido, a Apple encorajou os trabalhadores a alternar para outras posições de montagem e teste a cada seis semanas. Isso ajudou a manter o moral positivo e deu aos trabalhadores a oportunidade de aprender novas posições e adquirir novas habilidades.
A fábrica do Macintosh ofereceu um vislumbre de um futuro da produção de computadores em que os fabricantes poderiam reduza os custos de mão-de-obra e, ao mesmo tempo, produza rapidamente máquinas em quantidades inimagináveis apenas alguns anos antes. Mas a produção em grande escala de computadores Apple e da instalação de Fremont não duraria muito.
A seguir: Steve Jobs comete os mesmos erros na NeXT.
Luke Dormehl e Killian Bell contribuíram para este post.