Questo post sarebbe stato parte del mio nuovo libro, Tim Cook: il genio che ha portato Apple al livello successivo, ma è stato tagliato per la lunghezza. Nel corso della prossima settimana circa, pubblicheremo molte altre sezioni che sono state tagliate, concentrandosi principalmente sulle operazioni di produzione di Apple.
Steve Jobs ha sempre avuto un profondo fascino per le fabbriche automatizzate. È stato esposto per la prima volta a loro durante un viaggio in Giappone nel 1983. All'epoca, Apple aveva appena creato una nuova unità floppy chiamata Twiggy. Durante una visita alla fabbrica Apple a San Jose, tuttavia, Jobs si arrabbiò quando scoprì l'alto tasso di guasto delle unità Twiggy che Apple stava producendo. Più della metà è stata respinta. Jobs ha minacciato di licenziare tutti coloro che lavoravano in fabbrica
Questo post contiene link di affiliazione. Culto di Mac può guadagnare una commissione quando utilizzi i nostri link per acquistare articoli.
Ispirato da Alpi e Ford
Un'alternativa era utilizzare una nuova unità da 3,5 pollici sviluppata da Sony e prodotta da un piccolo fornitore giapponese chiamato
Elettronica Alpi. Quarant'anni dopo, le Alpi rimangono parte della catena di approvvigionamento di Apple. Jobs conosceva Yasuyuki Hirose, un ingegnere di Alps, che aveva incontrato al Fiera del computer della costa occidentale, la prima fiera di personal computer della Silicon Valley in cui Apple ha debuttato l'Apple II.Nel 1983, Jobs visitò la fabbrica di Alps in Giappone. A quel tempo, il Giappone stava vivendo una crescita economica sorprendente, in parte grazie alle sue fabbriche, che producevano automobili, microchip e walkman a una velocità sorprendente.
Secondo Yasuyuki Hirose, un ingegnere di floppy disk presso Alps, “Steve era particolarmente interessato ai processi di produzione. Nel 1983, ha fatto un giro della fabbrica automatizzata a Furukawa e ha posto molte domande”. (Alcuni anni dopo, quando Jobs aveva aperto una sua fabbrica automatizzata, aveva invitato Hirose a fargli visita. "Fu allora che capii cosa Steve aveva sempre voluto fare", ha detto Hirose.)
Jobs è rimasto colpito dal Giappone, un paese con cui ha avuto una storia d'amore per tutta la vita. Tuttavia, la sua spinta a costruire fabbriche automatizzate potrebbe anche essere stata in parte ispirata da uno degli eroi americani di Jobs: il pioniere dell'auto Henry Ford.
Le auto Ford hanno cambiato il mondo non solo per la tecnologia che hanno introdotto, ma anche perché erano abbastanza economiche da poter essere acquistate dalle masse. Nella sua spinta verso la produzione di massa, le auto Ford venivano assemblate in vaste fabbriche, dove le linee di assemblaggio dividevano il processo di produzione in fasi ripetibili. Grazie alle sue innovazioni, una delle auto di Henry Ford poteva essere assemblata in meno di un'ora.
Fabbrica automatizzata di Mac
Ci sono voluti solo 26 minuti per costruire un intero Macintosh nell'impianto di produzione altamente automatizzato aperto da Apple a Fremont, in California, nel gennaio 1984, meno di un anno dopo il viaggio di Jobs in Giappone.
Costruito su 120.000 piedi quadrati, l'impianto a 48233 Warm Springs Blvd è costato 20 milioni di dollari ed è stato un fiore all'occhiello di produzione automatizzata, progettata con l'obiettivo di produrre fino a un milione di unità del Macintosh $ 2.495 ogni singolo mese.
"Abbiamo un grande rispetto per la produzione giapponese", ha affermato l'allora presidente di Apple John Sculley. “Abbiamo deciso di essere uno dei principali attori nella tecnologia di produzione. In tre anni vogliamo essere bravi come i giapponesi”.
Quando Apple aveva abbastanza componenti nel suo inventario e la produzione era in pieno svolgimento, una nuova macchina usciva dalla catena di montaggio ogni ventisette secondi.
George Irwin, un ingegnere che ha contribuito a pianificare la struttura, che è stata paragonata a una gigantesca fabbrica di blocchi Lego a causa di avere così tante macchine, ognuna delle quali svolgeva un compito diverso, aveva l'obiettivo di ridurle a solo tredici secondi.
Nessun altro produttore di computer era in grado di eguagliare questo tipo di output in quel momento. Nello stabilimento Apple di Dallas, veniva prodotto un Apple IIe ogni sei minuti e il montaggio richiedeva molto più tempo.
"Prima che il Giappone si avvicini ai computer, vogliamo stare al passo con il gioco", ha detto Irwin alla rivista InfoWorld nel marzo 1984.

Foto: Terrence McCarthy, usata con permesso.
Come funzionava l'automazione
Ogni Macintosh era assemblato da otto componenti principali che potevano essere messi insieme in modo rapido e semplice. Le macchine viaggerebbero per la fabbrica sospese al soffitto sui ricchi binari rossi di un'an trasportatore sopraelevato e i lavoratori avevano ventidue secondi o meno per completare il loro ruolo prima che si spostasse su il prossimo.
Apple si è assicurata che nessun lavoratore dovesse raggiungere più di trenta pollici per le parti di cui aveva bisogno, che sono state consegnate a ciascuna stazione su un veicolo di guida automatizzato alto un metro.
Cinque di queste macchine, ciascuna del costo di $ 30.000, vagavano per lo stabilimento. I loro compiti sono stati assegnati da un occhio Polaroid che ha scansionato il magazzino e ha emesso un comando quando ha identificato un vassoio di componenti che doveva essere trasferito.
I vassoi stessi erano pieni di contenitori da cinquanta libbre, almeno quattromila dei quali erano impilati per diciotto livelli in qualsiasi momento.
L'impilatore di contenitori, un altro servizio di consegna automatizzata, ha fatto il giro della fabbrica su un binario, posizionando i contenitori nella posizione corretta.
Per montare circuiti e moduli sulle schede logiche sono state utilizzate macchine ad autoinserimento, mentre circa centoventi I computer Apple, principalmente l'Apple II e l'Apple III, furono impiegati come terminali per l'elaborazione della contabilità e dell'inventario dati.
Le richieste insolite di Jobs
Jobs ha chiesto che le macchine fossero dipinte con tonalità luminose e colorate, corrispondenti a quelle del logo Apple a strisce utilizzato all'epoca. Ma dopo aver passato così tanto tempo a esaminare le schegge di vernice, l'allora direttore di produzione di Apple, Matt Carter, le ha finalmente installate nel solito beige.
Jobs lo notò durante un tour della fabbrica, scrive il suo biografo, Walter Isaacson, e chiese che fossero ridipinti nei colori da lui richiesti. Carter ha obiettato e ha spiegato che la vernice potrebbe causare problemi alle macchine di precisione, e questo è stato dimostrato corretto quando una delle macchine più costose di Apple, dipinta di blu brillante e in seguito soprannominata "la follia di Steve", ha smesso di funzionare propriamente.
Carter si è dimesso a causa del disaccordo; "Ci voleva così tanta energia per combatterlo, e di solito si trattava di qualcosa di così inutile che alla fine ne avevo abbastanza", ha detto a Isaacson.
Carter è stato sostituito da Debi Coleman, l'ufficiale finanziario Macintosh che in precedenza aveva vinto il premio annuale del team per la persona che meglio tenne testa a Jobs, e ben presto anche lei si trovò coinvolta in un disaccordo sulla fabbrica dipingere.
Jobs aveva chiesto al direttore artistico di Apple, Clement Mok, di esprimere i suoi desideri che le pareti della fabbrica fossero dipinte di bianco.
"Non puoi dipingere una fabbrica di bianco puro", ha affermato Coleman, "ci sarà polvere e roba dappertutto".
"Non c'è bianco che sia troppo bianco per Steve", ha risposto Mok.
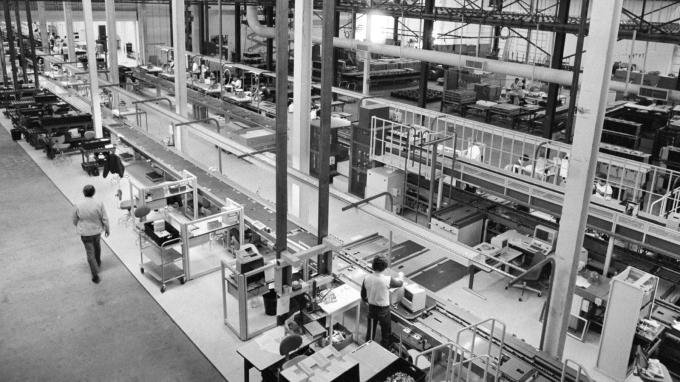
Foto: Terrence McCarthy, con permesso.
La pulizia è accanto alla Jobsiness
Pochi presidenti di società sarebbero ossessionati dal colore di una fabbrica e delle sue macchine come fece Jobs con la struttura Macintosh.
Voleva anche che fosse pulito e insisteva che questo fosse un modo per garantire "una passione per la perfezione", scrive Isaacson. "Andavo in fabbrica e mi mettevo un guanto bianco per controllare la polvere", ricorda Jobs. "Lo troverei ovunque: sulle macchine, sulla parte superiore degli scaffali, sul pavimento".
Jobs chiese a Coleman di ripulire la fabbrica. "Le ho detto che pensavo che dovremmo essere in grado di mangiare dal pavimento della fabbrica", ha continuato Jobs. "Non ha capito perché."
Automazione nel senso più puro
Pochissime attività richiedevano mani umane. Le macchine hanno eseguito oltre il 90 percento del processo di assemblaggio, con gli operai che sono intervenuti per riparare eventuali difetti, come ad esempio sostituzione di componenti difettosi o per eseguire i lavori che richiedono un tocco umano, come lucidare i loghi Apple apposti su ciascuno involucro.
Un rigoroso processo di test noto come "ciclo di burn-in", che consisteva nell'accendere ogni macchina e spegnimento ogni ora nell'arco di ventiquattro ore, è stato effettuato per garantire il corretto funzionamento di ogni chip.
"Altre aziende accendono il computer e lasciano che il loro computer si trovi lì", ha spiegato Sam Khoo, un direttore di produzione presso lo stabilimento Apple. InfoWorld. “Spegniamo e accendiamo di più i componenti. In questo modo i componenti difettosi appariranno subito.”
La struttura di Fremont era "automazione nel senso più puro", ha detto Irwin. Erano necessari meno di novanta lavoratori per ogni turno, ed erano separati da macchine gigantesche e vaste voragini di spazio che significavano che c'era pochissimo lavoro di squadra.
Nel tentativo di evitare che il loro lavoro diventi mondano e insopportabile, il che porterebbe senza dubbio all'alto turnover del personale che hanno sofferto altre fabbriche, Apple ha incoraggiato i lavoratori a ruotare in altre posizioni di assemblaggio e collaudo ogni sei settimane. Ciò ha contribuito a mantenere il morale positivo e ha dato ai lavoratori l'opportunità di apprendere nuove posizioni e acquisire nuove competenze.
La fabbrica Macintosh offriva uno sguardo a un futuro della produzione di computer in cui i produttori avrebbero potuto tagliare i costi del lavoro ma produrre rapidamente macchine in numeri impensabili solo pochi anni prima. Ma la produzione su larga scala di computer Apple e lo stabilimento di Fremont non sarebbero durati a lungo.
Prossimamente: Steve Jobs fa gli stessi errori alla NeXT.
Luke Dormehl e Killian Bell hanno contribuito a questo post.